Usually, when we try to shield a device or cabinet from electro-magnetic radiation, we encapsulate the sensitive equipment or the radiating source with metal. When this is not perfectly feasible we combine a variety of materials into an electrically conductive cage. Practical considerations are size and shape, permanently closed or re-openable and galvanic compatibility between materials.
In order to provide local shielding against EMI/RFI disturbances on your PCB a metal shielding protection can be applied. This is also known as a ‘shielding-can’. The assembly methods are either or both through-hole and surface-mount soldering processes. A new innovation is the use of SMD clips in which the PCB shielding can be snapped in. This technology makes both prototyping and the production process much more efficient. A range of standard sizes is available. Nevertheless creating a dedicated geometry is an uncomplicated process which can be utilized with a small budget. Naturally, designs comprising more complexity, like multi-cavity, retractable lid, sloped edges and engraving will not form any problem to us.
Engineered laminated foils can be used as EMI and ESD shielding or ground plane. Depending on the layer-stack, the thickness ranges from 0.1 – 0.6 [mm]. Examples are a PVC isolation layer and 1 or 2 conductive layers, one or two PSA layers with or without peel away mask. These laminates can be supplied in every thinkable shape, including slits, notches and creases.
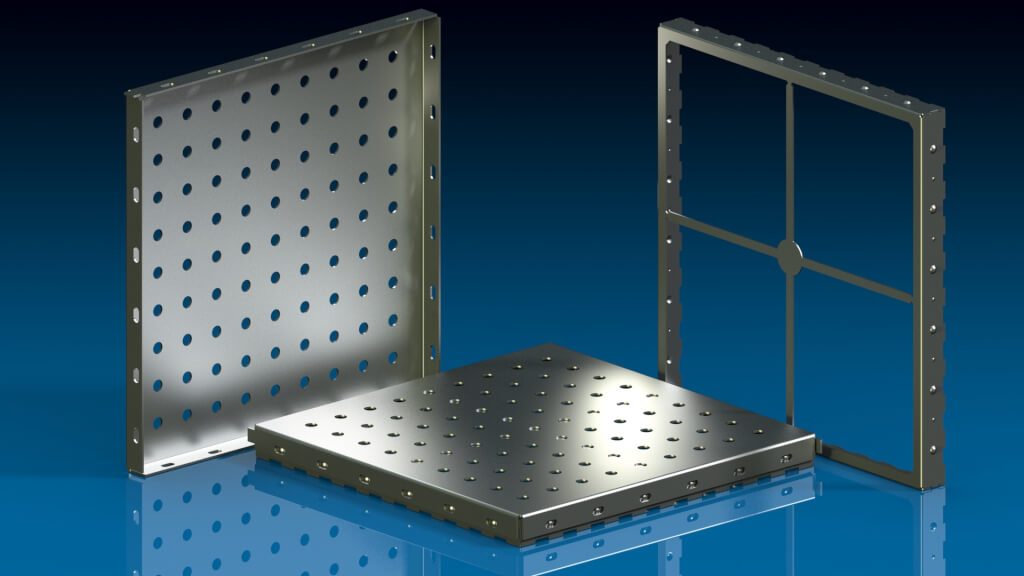
When production numbers increase, the use of injection molded electrically conductive plastics have tremendous benefits. Using this technology it becomes relatively simple to design electromagnetically isolated compartments between circuits that potentially influence each other.
The cables on your device form a set of undesired “antennae”. Cable shielding is usually applied to reduce emissions and to increase immunity. Since, in the field, so many cable types and configurations are being applied we make it somewhat easier for you with a selection of universally applicable cable shielding techniques.
Our conductive foils and tape are being produced from copper, aluminum or tinned copper. As a standard, the foils and tapes are backed with highly conductive pressure sensitive adhesive on one or both sides of the material.
In order to ease your procurement and production process we have the facilities to die-cut the material. We supply virtually every producible geometrical shape including slits, notches and creases.
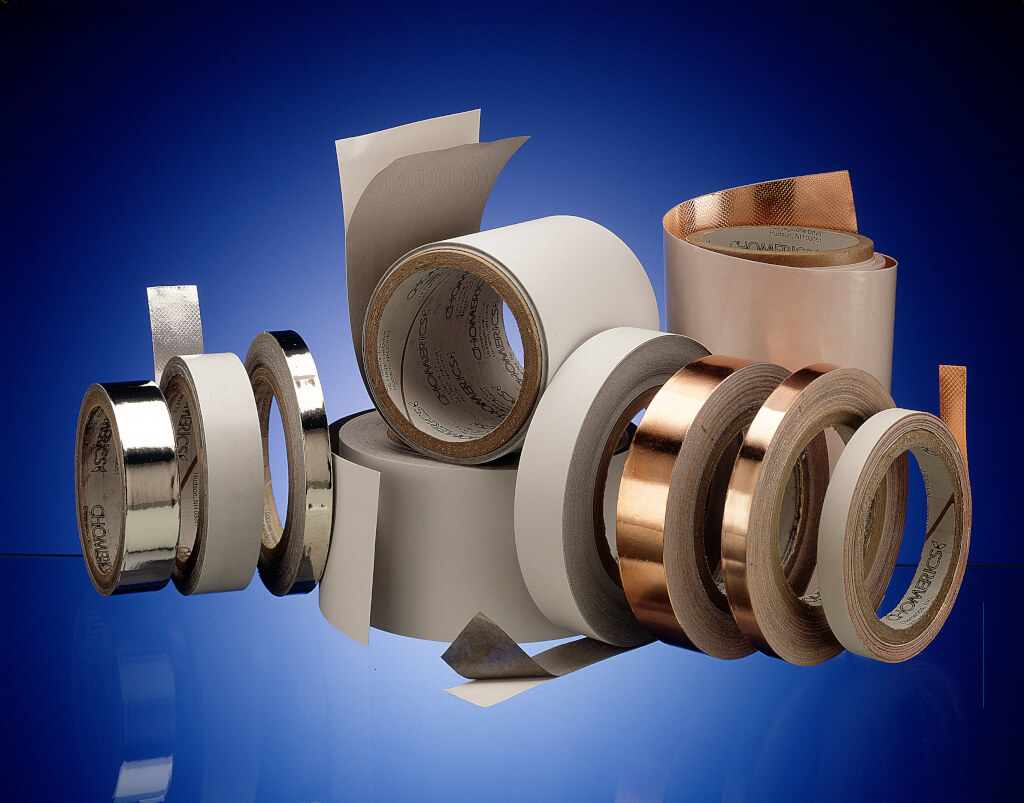
Our electrically conductive textiles are tear resistant, flexible and lightweight. They are easily formed and shaped to use in a wide range of EMI shielding applications.
Examples of applications are:
- RF shielding tents
- Shielding pouches for mobile devices
- Curtains to dampen RFID signals in order to manage detection and false-detection in shops and warehouses
- Clothing and hand gloves where the antibacterial properties of silver is being utilized
The base material for our conductive textiles is silver coated polyamide. This can be supplied in several forms, such as:
- Yarns and twisted yarn
- Sewing thread
- Fibers can be easily mixed with all other natural and synthetic fibers so they can be applied in, for example, carpets where no static charge is allowed to accumulate, such as in an airplane
- Cable sleeves and cable shielding
- Velcro
- Zippers
In addition, we supply electrically conductive textile tape. This ultra-flexible tape has an adhesion layer and is suitable to be used in a sewing process as well. The material is tear-resistant, flexible and light weight. The conductive properties are being obtained by using silver or nickel.
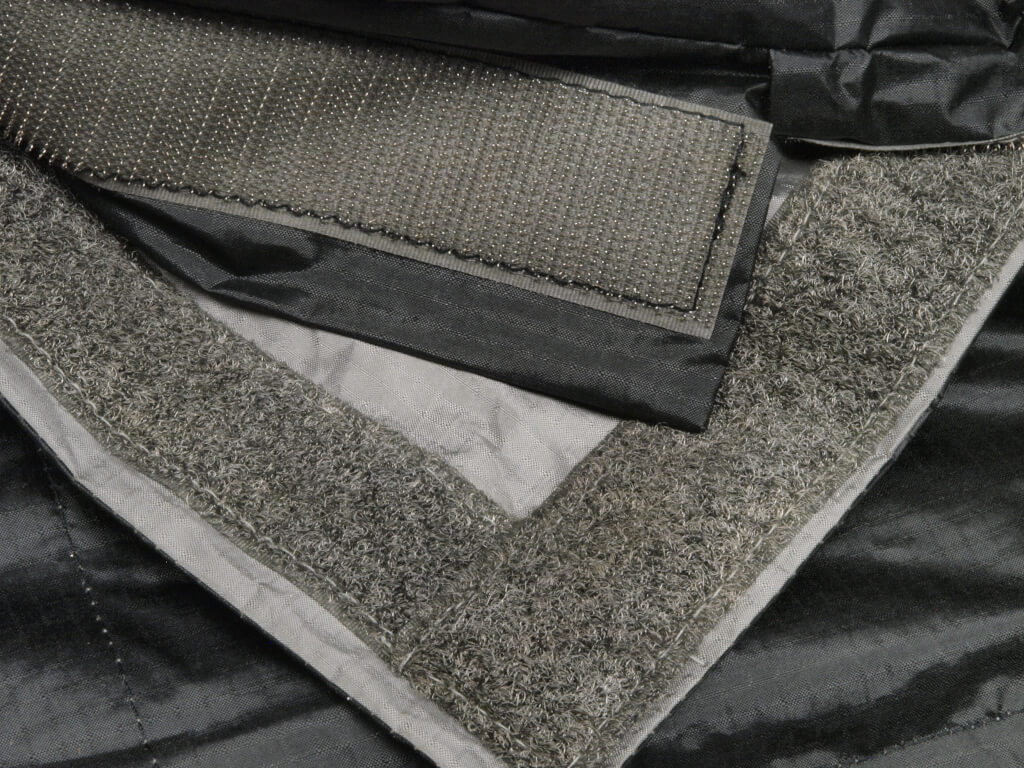
In order to shield an entire room discretely and sleek, we provide electrically conductive wallpaper. The wallpaper is being applied similar to conventional wallpaper. The electrical connections are being formed using electrically conductive ultra-flexible textile-tape and in addition an earth-connection is being made.
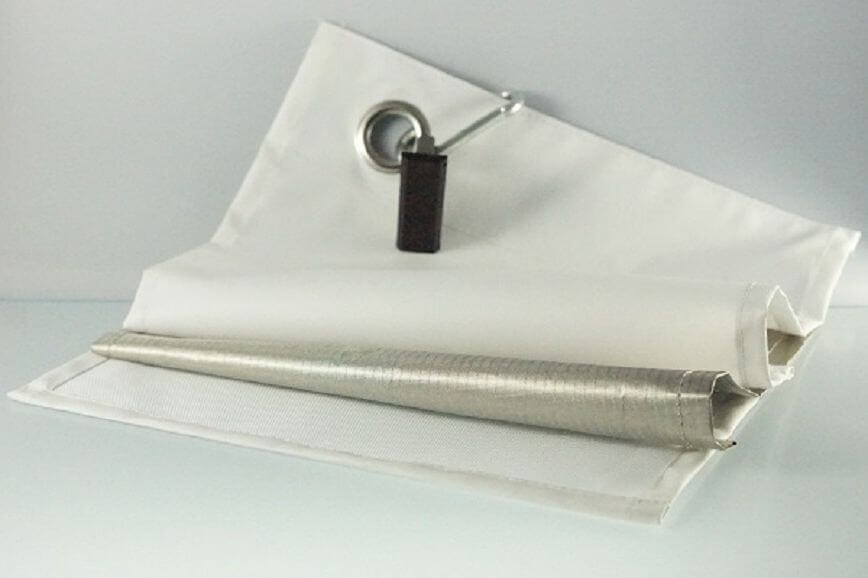
Occasionally a shielded chamber requires an aperture (for illumination or as a see-through) while, from electrical point of view, an uninterrupted surface is required. This is made possible using EMI shielding windows.
Using a sophisticated production process several types of metal mesh can be inserted invisibly into a window. Based on extensive measurements and experiments we can offer the optimal solution for the most demanding applications, such as shielding of (tempest) monitors, displays, measurement chambers and shelters.
To make sure an optimal EMI shielding is achieved, a conductive bus bar is applied around the entire perimeter of the window, contacting the mesh inside. According to your desired geometry, every bus bar shape can be applied. In addition a special welding technique makes it possible to create an electric contact at any desired position in the window surface.
These EMI shielding windows can be supplied with additional hardening and/or anti-glare and anti-reflection surface treatments.
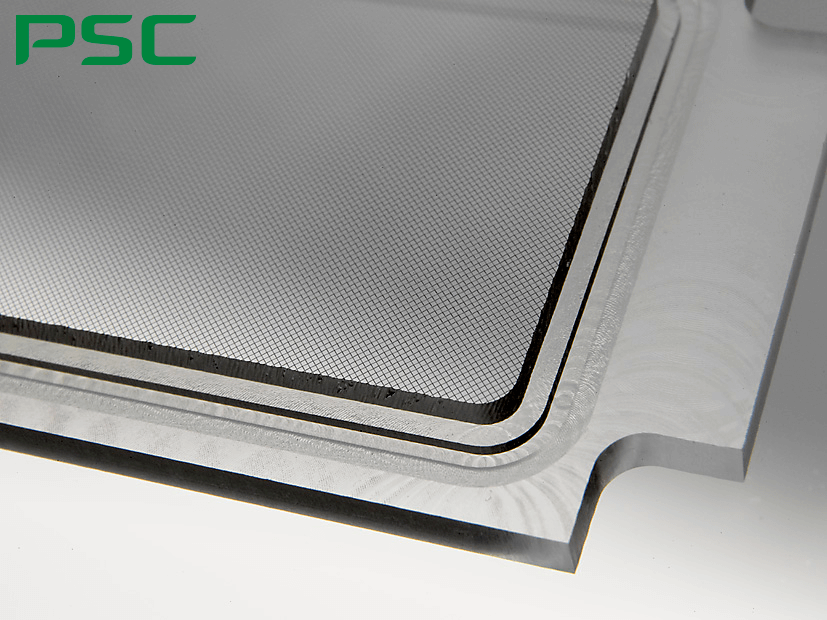
Although a shielded chamber requires uninterrupted conductive surfaces the chamber usually also needs some sort of interruption for ventilation purposes. In order to establish optimal management of (thermal) ventilation you can apply our EMI-shielding (honeycomb) vents. The combination of a maximum damping for EMC purposes and a minimum drop of pressure for airflow purposes makes these honeycomb vents the highest quality products in their sort.
Due to the more than 95 [%] open area the honeycombs have an optimal relation between mass and volume. In addition to the standard honeycomb we offer omni-cell configurations in which two parallel half thickness honeycomb panels are stacked at different angles. Potential polarization effects are eliminated and an even deeper attenuation is being achieved.
The vent opening can be cylindrical to accommodate a fan or rectangular up to 610 x 610 [mm] beyond that specials are possible. A variety of frame styles is available in order to mount the vent on top, built in or sunken into your chamber or cabinet. Depending on your application the vents are being supplied with the appropriate gasket being integrated into the frame.
In order to optimally suit your application feel free to contact us when it comes to:
- Tempest
- Coating (conductive or non-conductive)
- Fire retardancy (Intumescent coating)
- Forced airflow
- Air filtering EMI shielding
- Water resistance / drip proof
- Corrosion resistance
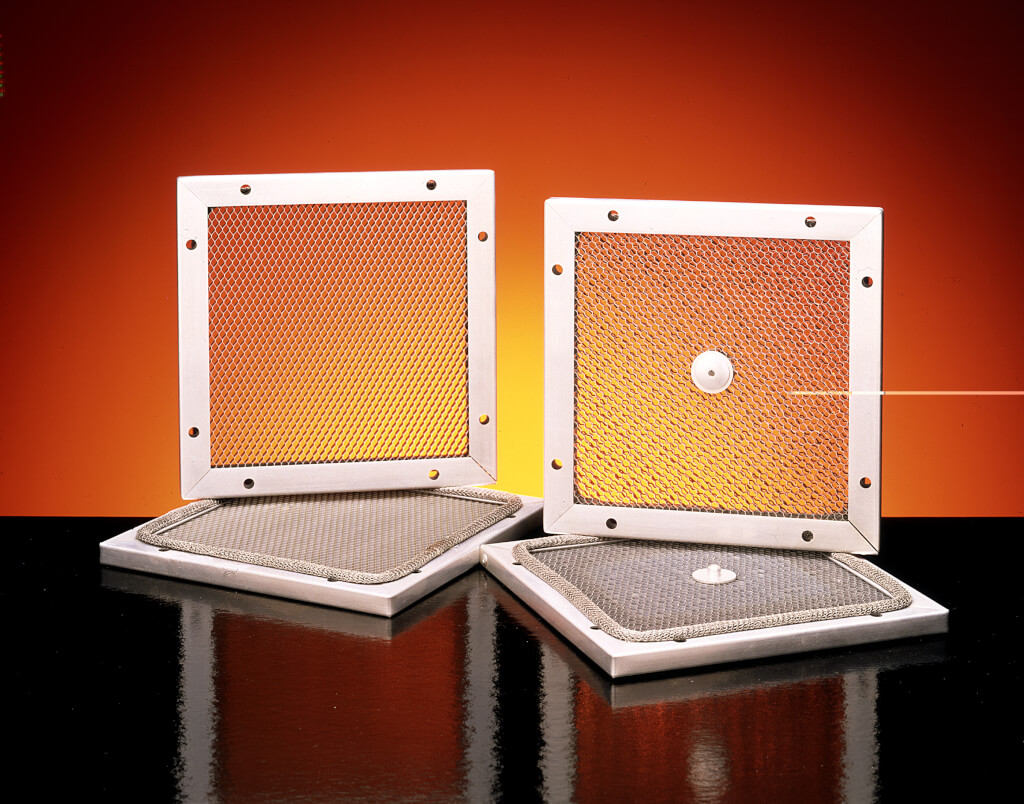